ଉତ୍ପାଦନ କ୍ଷେତ୍ର ସବୁଠାରୁ ଗତିଶୀଳ ଶିଳ୍ପ ମଧ୍ୟରୁ ଗୋଟିଏ। ଆଜି, ସାମଗ୍ରିକ ସଠିକତା ଏବଂ ସଠିକତା ଏବଂ ତାର EDM ଭଳି ପ୍ରକ୍ରିୟାଗୁଡ଼ିକୁ ବୃଦ୍ଧି କରିବା ପାଇଁ ଏକ ନିରନ୍ତର ପ୍ରୟାସ କରାଯାଉଛି ଯାହା ଶିଳ୍ପ ପାଇଁ ପରିବର୍ତ୍ତନକାରୀଠାରୁ କମ୍ ନୁହେଁ।
ତେବେ, Wire EDM ପ୍ରକୃତରେ କ'ଣ, ଏବଂ ଏହାକୁ ଉତ୍ପାଦନ କ୍ଷେତ୍ର ପାଇଁ ଏକ ପରିବର୍ତ୍ତନକାରୀ କାହିଁକି ବିବେଚନା କରାଯାଏ? ନିମ୍ନଲିଖିତ ଲେଖାଟି ବିଭିନ୍ନ ଶିଳ୍ପରେ ପ୍ରୟୋଗ ସହିତ ଏହି ସୁସଂସ୍କୃତ ଉତ୍ପାଦନ କୌଶଳର ମୌଳିକ ବିଷୟଗୁଡ଼ିକ ଉପରେ ଏକ ନଜର ପକାଇବ।
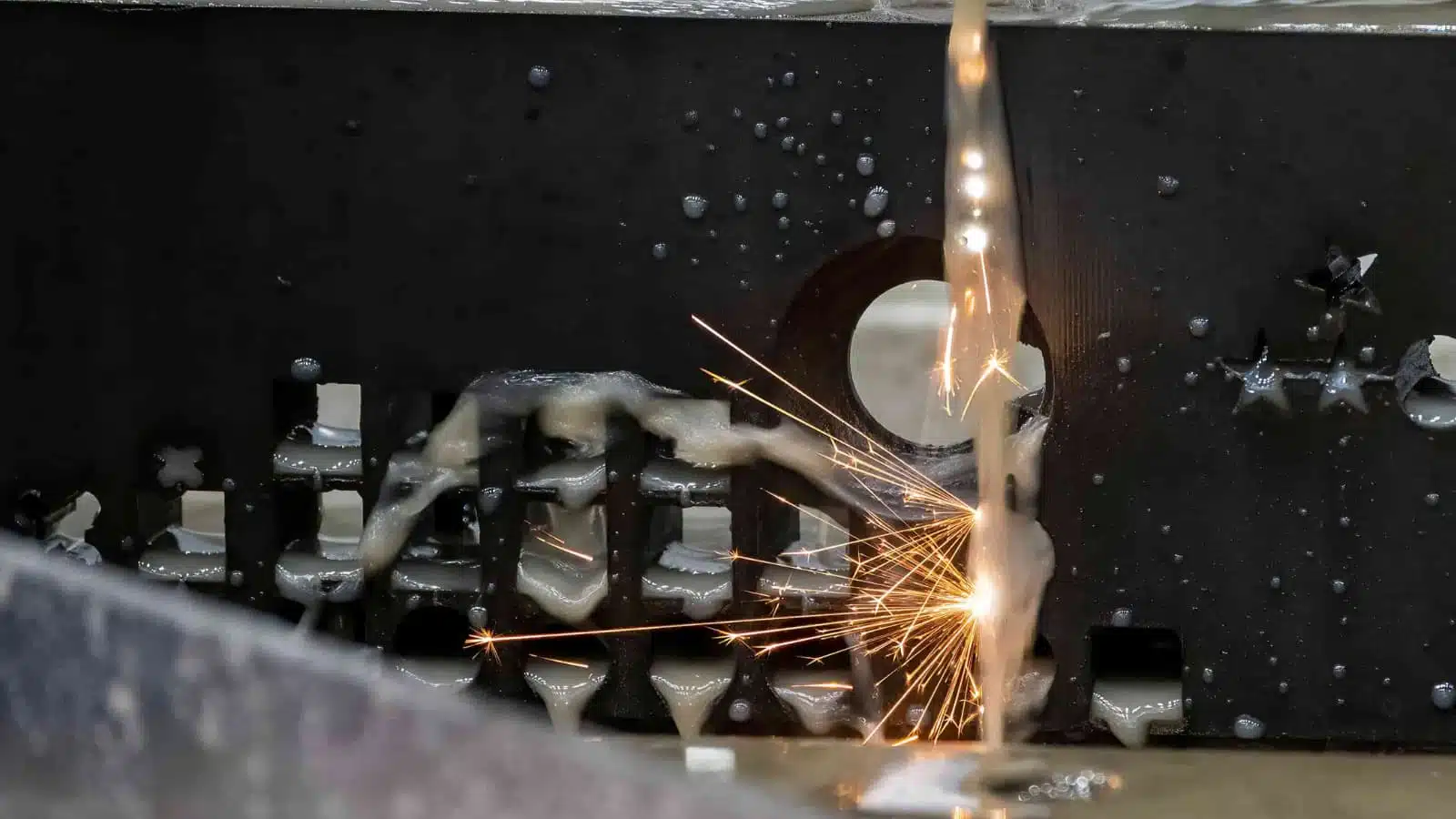
ୱାୟାର EDM ର ଏକ ସଂକ୍ଷିପ୍ତ ପରିଚୟ
୧୯୪୦ ଦଶକରେ ଦୁଇଜଣ ସୋଭିଏତ୍ ବୈଜ୍ଞାନିକଙ୍କ ଦ୍ୱାରା ୱାୟାର ଇଲେକ୍ଟ୍ରିକାଲ୍ ଡିସଚାର୍ଜ ମେସିନିଂ (EDM) ଆରମ୍ଭ ହୋଇଥିଲା, ଯେଉଁମାନେ ପ୍ରଥମେ ବୈଦ୍ୟୁତିକ ଡିସଚାର୍ଜ ସହିତ ଧାତୁକୁ କ୍ଷୟ କରିଥିଲେ। 60 ଏବଂ 80 ଦଶକରେ ଏହି ପ୍ରଯୁକ୍ତିବିଦ୍ୟାରେ ଗୁରୁତ୍ୱପୂର୍ଣ୍ଣ ଉନ୍ନତି ଘଟିଥିଲା, ଯାହା ଉତ୍ପାଦନ କ୍ଷେତ୍ରରେ ବାଣିଜ୍ୟିକ ଭାବରେ ପ୍ରଚଳିତ ହୋଇଥିଲା। 90 ଦଶକର ଶେଷ ସୁଦ୍ଧା, IT ଏବଂ CNC ଉନ୍ନତି ସହିତ, ୱାୟାର EDM ମେସିନଗୁଡ଼ିକ ଅଧିକ କମ୍ପ୍ୟୁଟରୀକରଣ ହୋଇଗଲା, ଯାହା ସେମାନଙ୍କର ଦକ୍ଷତା ଏବଂ ସଠିକତାକୁ ବୃଦ୍ଧି କଲା।
ଆଜି, ୱାୟାର EDM ଏରୋସ୍ପେସ୍, ଅଟୋମୋଟିଭ୍ ଏବଂ ମେଡିକାଲ୍ ଭଳି ଶିଳ୍ପରେ ଅତ୍ୟାବଶ୍ୟକ, ଯାହା ପାରମ୍ପରିକ ମେସିନିଂ ପଦ୍ଧତି ସହିତ ଅତୁଳନୀୟ ଜଟିଳ ଡିଜାଇନ୍ ଏବଂ ଜଟିଳ ରୂପ ପ୍ରଦାନ କରିବା ପାଇଁ ଜଣାଶୁଣା।
ଦି ୱାୟାର EDM ପ୍ରକ୍ରିୟା
ୱାୟାର ଇଲେକ୍ଟ୍ରିକାଲ୍ ଡିସଚାର୍ଜ ମେସିନିଂ (EDM) ଏକ ସଠିକ୍ ପଦ୍ଧତି ଯାହା ଏକ ୱର୍କପିସର କ୍ଷୁଦ୍ର ଅଂଶଗୁଡ଼ିକୁ ତରଳାଇବା ପାଇଁ ନିୟନ୍ତ୍ରିତ ବୈଦ୍ୟୁତିକ ସ୍ପାର୍କ ବ୍ୟବହାର କରେ। ସାଧାରଣତଃ ପିତ୍ତଳ କିମ୍ବା ଜିଙ୍କ-ଆବରଣଯୁକ୍ତ ସାମଗ୍ରୀରେ ତିଆରି ତାର ଇଲେକ୍ଟ୍ରୋଡ୍ ଏହି ସ୍ପାର୍କ ସୃଷ୍ଟି କରେ ଏବଂ ଏକ ପୂର୍ବ-ନିର୍ଦ୍ଧାରିତ ପଥରେ ଗତି କରେ। ଏହାର ଲାଭ? ଏହା ଶାରୀରିକ ସମ୍ପର୍କ ବିନା କାମ କରେ, ୱର୍କପିସ୍ ଏବଂ ଉପକରଣ ଉଭୟରେ କୌଣସି କ୍ଷତି କିମ୍ବା ଚିହ୍ନକୁ ରୋକିଥାଏ।
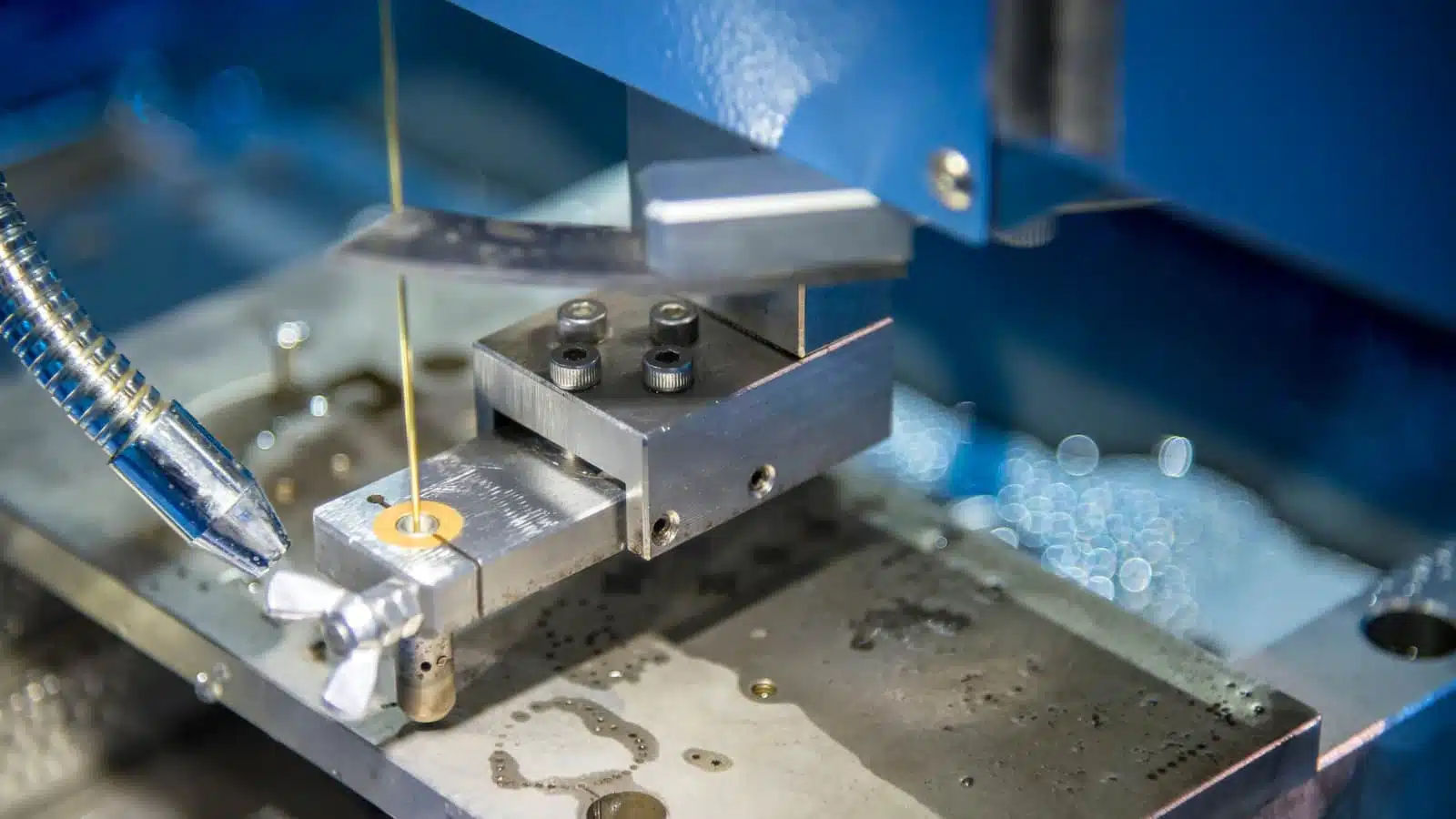
EDM କିପରି କାମ କରେ
EDM ବୈଦ୍ୟୁତିକ ନିର୍ଗମନରୁ ଉତ୍ତାପ ଶକ୍ତି ଉପରେ ନିର୍ଭର କରେ। ଏହି ନିର୍ଗମନ କାର୍ଯ୍ୟକ୍ଷେତ୍ରକୁ ଏହାର ତରଳାଇବା ବିନ୍ଦୁ ପର୍ଯ୍ୟନ୍ତ ଗରମ କରେ, କ୍ଷୁଦ୍ର ପ୍ଲାଜ୍ମା ଚ୍ୟାନେଲ ତିଆରି କରେ। ଏହି ଚ୍ୟାନେଲଗୁଡ଼ିକ, ପ୍ରାୟତଃ ମାଇକ୍ରୋମିଟର ଆକାରର, ଶୀଘ୍ର ଅଦୃଶ୍ୟ ହୋଇଯାଇପାରେ।
EDM ପ୍ରକ୍ରିୟା ଏକ ଡାଇଇଲେକ୍ଟ୍ରିକ୍ ମାଧ୍ୟମରେ ଘଟେ, ସାଧାରଣତଃ ଡିଆୟୋନାଇଜଡ୍ ପାଣିରେ। ଏହି ତରଳ ପଦାର୍ଥ କାର୍ଯ୍ୟକ୍ଷେତ୍ରକୁ ଥଣ୍ଡା କରେ ଏବଂ ବାଷ୍ପୀକୃତ ସାମଗ୍ରୀକୁ ବାହାର କରିଦିଏ, ଯାହା ନିରନ୍ତର ମେସିନିଂରେ ସାହାଯ୍ୟ କରେ।
ତାର ଇଲେକ୍ଟ୍ରୋଡର ଗୁରୁତ୍ୱ
କଟର ଏବଂ କଣ୍ଡକ୍ଟର ଭାବରେ କାର୍ଯ୍ୟ କରୁଥିବା ଏହି ତାର ଇଲେକ୍ଟ୍ରୋଡ୍ ଅତ୍ୟନ୍ତ ଗୁରୁତ୍ୱପୂର୍ଣ୍ଣ। ପିତ୍ତଳ କିମ୍ବା ଦସ୍ତା ଭଳି ସାମଗ୍ରୀ ସହିତ ଆବୃତ, ଏହା ଉଚ୍ଚ ତାପମାତ୍ରାରେ ପ୍ରତିକ୍ରିୟାକୁ ପ୍ରତିରୋଧ କରେ। ଏକ କମ୍ପ୍ୟୁଟର ଦ୍ୱାରା ନିୟନ୍ତ୍ରିତ, ଏହା ସର୍ବନିମ୍ନ ବିକୃତି ଏବଂ ଉଚ୍ଚ ସଠିକତା ସହିତ ସଠିକ୍ କଟ୍ ସୁନିଶ୍ଚିତ କରେ।
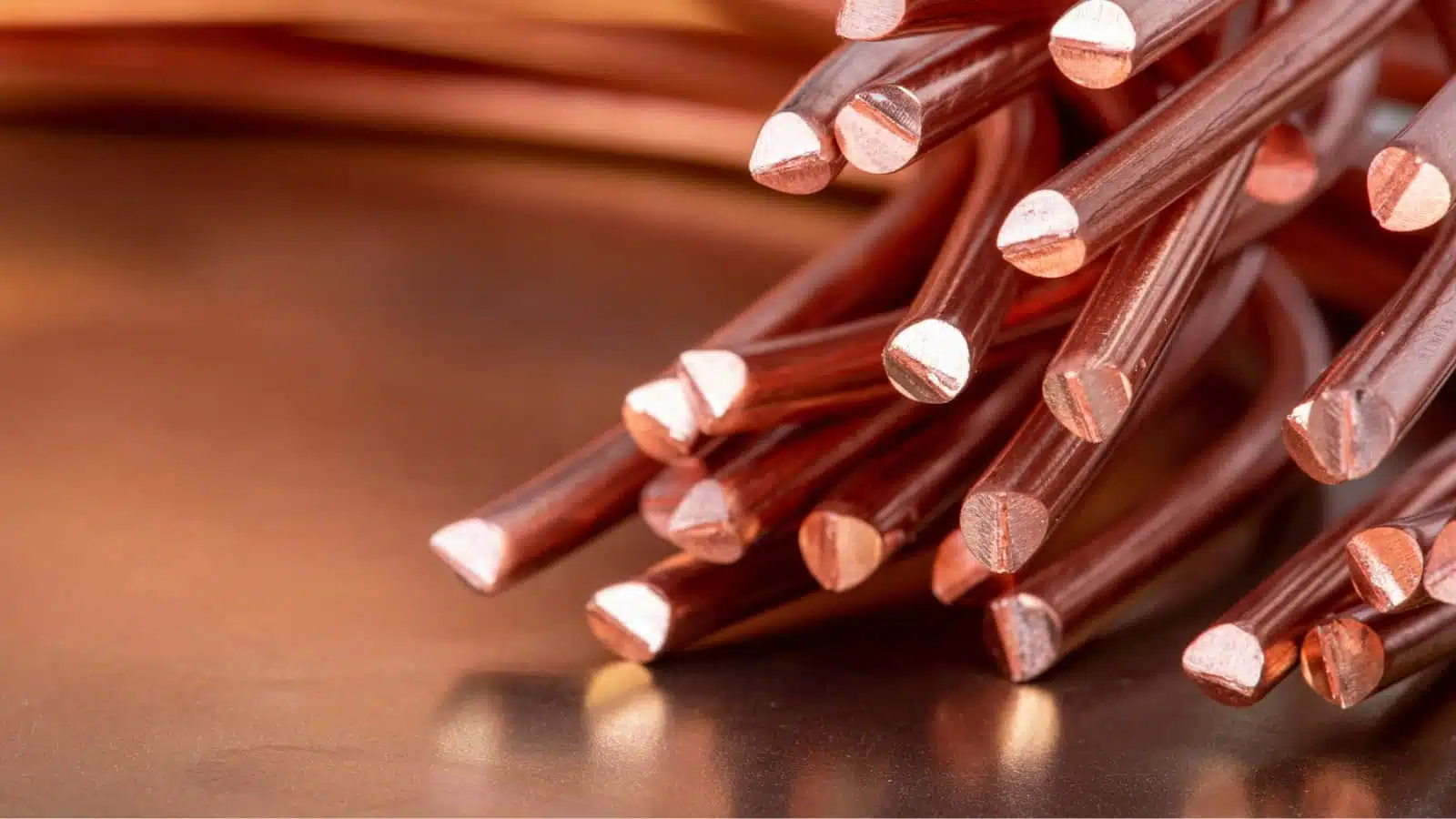
ତାର EDM ପାଇଁ ସହନଶୀଳତା
ତାର କାଟିବା ସବୁଠାରୁ ସଠିକ୍ ଉତ୍ପାଦନ ପ୍ରକ୍ରିୟା ମଧ୍ୟରୁ ଗୋଟିଏ। ତେଣୁ, କଡ଼ା ସହନଶୀଳତା ଏହା ପାଇଁ ସାଧାରଣ ନୁହେଁ। ପ୍ରକୃତ ସହନଶୀଳତା ପ୍ରକଳ୍ପର ଜଟିଳତା, ମେସିନିଂ କ୍ଷମତା ଏବଂ ଅପରେଟରଙ୍କ ଦକ୍ଷତା ସମେତ ଅନେକ କାରଣ ଉପରେ ନିର୍ଭର କରେ।
ତଥାପି, ମାନକ ଏବଂ ଗ୍ରହଣୀୟ ସହନଶୀଳତା ଏକ ଶିଳ୍ପ ମାନଦଣ୍ଡ ଯାହାକୁ ଅନେକ ନିର୍ମାତା ଅନୁସରଣ କରନ୍ତି।
ମାନକ ସହନଶୀଳତା ଏବଂ ସୂକ୍ଷ୍ମ ସହନଶୀଳତା
ମାନକ ସହନଶୀଳତା
ରେଖୀୟ ସହନଶୀଳତା: ସାଧାରଣତଃ ±0.005 ରୁ ±0.001 ଇଞ୍ଚ (0.127 ରୁ 0.0254 ମିମି) ପର୍ଯ୍ୟନ୍ତ ହୋଇଥାଏ, ଯାହା ଗାତ, ସ୍ଲଟ୍ କିମ୍ବା ପ୍ରୋଫାଇଲ୍ ଭଳି ବୈଶିଷ୍ଟ୍ୟ ପାଇଁ ଅନୁମତିପ୍ରାପ୍ତ ବିଚ୍ୟୁତିକୁ ସୂଚିତ କରେ।
ଗାତ ବ୍ୟାସ ସହନଶୀଳତା: ସାଧାରଣତଃ ±0.0005 ରୁ ±0.001 ଇଞ୍ଚ (0.0127 ରୁ 0.0254 ମିମି) ମଧ୍ୟରେ, ମେସିନ୍ ହୋଇଥିବା ଗାତଗୁଡ଼ିକ ନିର୍ଦ୍ଦିଷ୍ଟ ବ୍ୟାସ ମଧ୍ୟରେ ରହିବାକୁ ନିଶ୍ଚିତ କରେ।
ଉତ୍ତମ ସହନଶୀଳତା
ରେଖୀୟ ସହନଶୀଳତା: ମାଇକ୍ରୋନ ସ୍ତରରେ ସଠିକତା ହାସଲ କରେ, ସାଧାରଣତଃ ±0.0002 ରୁ ±0.0001 ଇଞ୍ଚ (0.0051 ରୁ 0.00254 ମିମି) ପର୍ଯ୍ୟନ୍ତ, ସର୍ବାଧିକ ସଠିକତା ଆବଶ୍ୟକ କରୁଥିବା ପ୍ରୟୋଗ ପାଇଁ ଗୁରୁତ୍ୱପୂର୍ଣ୍ଣ।
ଗାତ ବ୍ୟାସ ସହନଶୀଳତା: ±0.0001 ରୁ ±0.00005 ଇଞ୍ଚ (0.00254 ରୁ 0.00127 ମିମି) ପର୍ଯ୍ୟନ୍ତ, ଯାହା Wire EDM ର ଅସାଧାରଣ ସଠିକତାକୁ ଉଲ୍ଲେଖ କରେ।
ତାର EDM ରେ ସହନଶୀଳତାକୁ ପ୍ରଭାବିତ କରୁଥିବା କାରକଗୁଡ଼ିକ
ତାର EDM ଏହାର ମାଇକ୍ରୋନ-ସ୍ତରୀୟ ସଠିକତା ପାଇଁ ପ୍ରସିଦ୍ଧ, ଏହାକୁ ଜଟିଳ ପ୍ରୟୋଗ ପାଇଁ ଆଦର୍ଶ କରିଥାଏ। ତଥାପି, ଏହାର ସଠିକତା ସ୍ଥିର ନୁହେଁ ଏବଂ ଅନେକ କାରଣ ଉପରେ ନିର୍ଭର କରେ:
• ମେସିନ୍ ସ୍ଥିରତା: ଏକ ସ୍ଥିର ମେସିନ୍ କାଟିବା କାର୍ଯ୍ୟରେ ଉତ୍ତମ ସଠିକତା ସୁନିଶ୍ଚିତ କରେ।
•ତାର ଗୁଣବତ୍ତା ଏବଂ ବ୍ୟାସ: ଏହାର ଶୁଦ୍ଧତା, ବ୍ୟାସ ଏବଂ ବୈଦ୍ୟୁତିକ ଗୁଣଗୁଡ଼ିକ ମେସିନିଂ ପ୍ରକ୍ରିୟାକୁ ପ୍ରଭାବିତ କରେ। ସର୍ବୋତ୍ତମ ଫଳାଫଳ ପାଇଁ ତାର ଗୁଣବତ୍ତା ଏବଂ ବ୍ୟାସ ମଧ୍ୟରେ ସନ୍ତୁଳନ ଆବଶ୍ୟକ।
•କାର୍ଯ୍ୟକ୍ଷେତ୍ର ସାମଗ୍ରୀ: ଯଦିଓ କିଛି ସାମଗ୍ରୀ ମେସିନ ପାଇଁ ଅଧିକ ସୁଲଭ, ସାମଗ୍ରୀ ପସନ୍ଦ ପ୍ରୟୋଗର ଆବଶ୍ୟକତା ସହିତ ସମନ୍ୱିତ ହେବା ଉଚିତ।
•ଫ୍ଲସ୍ ଅବସ୍ଥା: ଡାଇଇଲେକ୍ଟ୍ରିକ୍ ମାଧ୍ୟମର ପ୍ରବାହ, ମେସିନିଂ ପ୍ରକ୍ରିୟାର ଗୁଣବତ୍ତା ଉପରେ ପ୍ରଭାବ ପକାଏ, ସାମଗ୍ରୀ ଅପସାରଣ, ସ୍ଥିର ବୈଦ୍ୟୁତିକ ନିର୍ଗମନ ଏବଂ ପ୍ରଭାବଶାଳୀ ତାପ ଅପଚୟରେ ସାହାଯ୍ୟ କରେ।
• ମେସିନ୍ କାଲିବ୍ରେସନ୍ ଏବଂ ରକ୍ଷଣାବେକ୍ଷଣ: ମେସିନ୍ ର କ୍ଷମତା ଅତ୍ୟନ୍ତ ଗୁରୁତ୍ୱପୂର୍ଣ୍ଣ। ସର୍ବୋତ୍ତମ ସହନଶୀଳତା ହାସଲ କରିବା ପାଇଁ ଦକ୍ଷ ଅପରେଟରମାନଙ୍କ ସହିତ ଉତ୍କୃଷ୍ଟ ମେସିନ୍ ଅତ୍ୟନ୍ତ ଜରୁରୀ।
•ତାପଜ ସ୍ଥିରତା: ତାର EDM ର ଜ୍ଞାତ ସଠିକତା ବଜାୟ ରଖିବା ପାଇଁ, ନିୟନ୍ତ୍ରିତ ବୈଦ୍ୟୁତିକ ଆର୍କ ଅତ୍ୟନ୍ତ ଗୁରୁତ୍ୱପୂର୍ଣ୍ଣ। ସ୍ଥିର ଅବସ୍ଥାର ଗୁରୁତ୍ୱ ଉପରେ ଗୁରୁତ୍ୱ ଦେଇ ତାପଜ ଅସ୍ଥିରତା ସଠିକତାକୁ ବିପଦରେ ପକାଇପାରେ।
ତାର କାଟିବା ପାଇଁ ସବୁଠାରୁ ଉପଯୁକ୍ତ ସାମଗ୍ରୀ
ଲୌହ ଧାତୁ
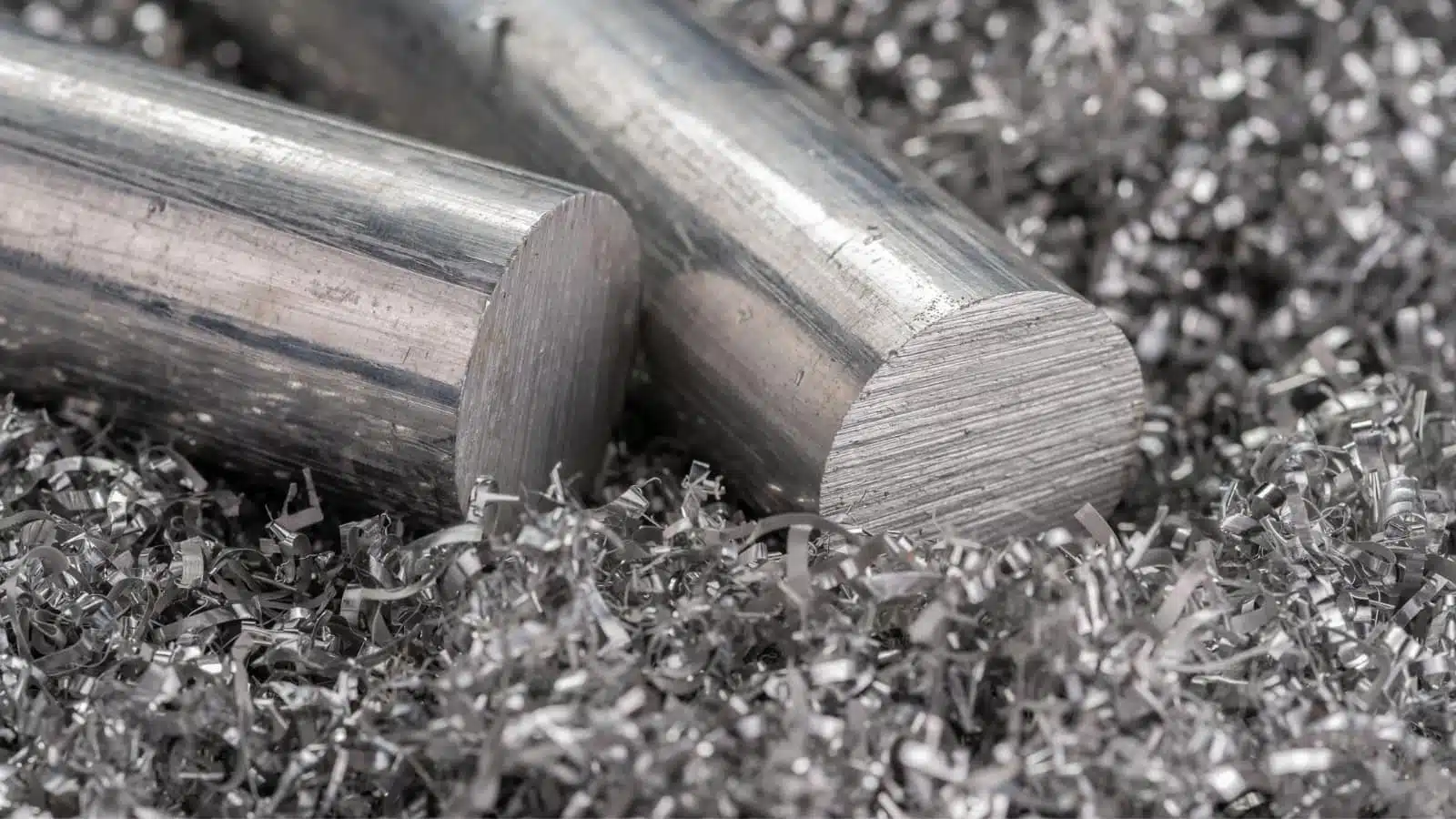
ଷ୍ଟେନଲେସ୍ ଷ୍ଟିଲ୍
ଏହା ସ୍ଥାୟୀତ୍ୱ ସହିତ ଉତ୍କୃଷ୍ଟ ବୈଦ୍ୟୁତିକ ପରିବାହିତାକୁ ମିଶ୍ରଣ କରିଥାଏ। କ୍ଷୟ ପ୍ରତିରୋଧ କରିବାର ଏହାର କ୍ଷମତା ଏହାକୁ ବିଭିନ୍ନ ଶିଳ୍ପରେ ଏକ ଆବଶ୍ୟକୀୟ ସାମଗ୍ରୀ କରିଥାଏ। ମେସିନିଂ ପରିପ୍ରେକ୍ଷୀରେ, ସଠିକ୍ ଏବଂ ବିସ୍ତୃତ ଡିଜାଇନ୍ ସହିତ ଏହାର ସୁସଙ୍ଗତତା ସ୍ପଷ୍ଟ ଭାବରେ ଦେଖାଯାଏ।
ଟୁଲ୍ ଷ୍ଟିଲ୍
ଏହାର କଠିନ ଗୁଣ ପାଇଁ ପ୍ରସିଦ୍ଧ, ଉପକରଣ ଇସ୍ପାତ ଅନେକ ଭାରୀ-କର୍ତ୍ତବ୍ୟ ଉପକରଣ ଏବଂ ସଠିକ ଅଂଶର ମେରୁଦଣ୍ଡ। ଏହାର ଅନ୍ତର୍ନିହିତ କଠିନତା, ଯେତେବେଳେ ଏହାର ବୈଦ୍ୟୁତିକ ଗୁଣ ସହିତ ଯୋଡାଯାଏ, ଏହାକୁ ଜଟିଳ ବିବରଣୀ ଏବଂ ଦୀର୍ଘସ୍ଥାୟୀ ତୀକ୍ଷ୍ଣତା ପାଇଁ ଏକ ପ୍ରମୁଖ ପ୍ରାର୍ଥୀ କରିଥାଏ।
କାର୍ବନ ଷ୍ଟିଲ୍
ଧାତୁ କ୍ଷେତ୍ରରେ ଏକ ବହୁମୁଖୀ ଖେଳାଳି, କାର୍ବନ ଇସ୍ପାତ, ଯଦିଓ ଏହାର ପ୍ରତିପକ୍ଷ ତୁଳନାରେ କମ୍ ମେସିନେବଲ୍, ସଠିକ୍ ଇଲେକ୍ଟ୍ରୋଡ୍ ପସନ୍ଦ ଏବଂ କାର୍ଯ୍ୟକ୍ଷମ ପାରାମିଟର ସହିତ ଏହାକୁ ସିଦ୍ଧତା ସହିତ ପ୍ରସ୍ତୁତ କରାଯାଇପାରିବ। ଏହାର ସୁଲଭତା ଏବଂ ଏହାର କାର୍ଯ୍ୟଦକ୍ଷତା ଏହାକୁ ଅନେକ ଶିଳ୍ପରେ ଏକ ପ୍ରମୁଖ କାରଣ କରିଥାଏ।
ମିଶ୍ରଧାତୁ ଇସ୍ପାତ
ଉପାଦାନଗୁଡ଼ିକର ମିଶ୍ରଣ, ଆଲୟ ଷ୍ଟିଲର କାର୍ଯ୍ୟଦକ୍ଷତା ଏହାର ଉପାଦାନଗୁଡ଼ିକର ଏକ ଟେପେଷ୍ଟ୍ରି। ଏହାର ଅନନ୍ୟ ମିଶ୍ରଣ ଉପରେ ନିର୍ଭର କରି, ଏହା ଶକ୍ତି, ସ୍ଥାୟୀତ୍ୱ ଏବଂ ମେସିନ୍ କ୍ଷମତା ପ୍ରଦାନ କରିପାରିବ, ଏହାକୁ ବିଭିନ୍ନ ପ୍ରୟୋଗ ପାଇଁ ଏକ ଗତିଶୀଳ ପସନ୍ଦ କରିଥାଏ।
ଅଣ-ଲୌହ ଧାତୁ
ଟାଇଟାନିୟମ୍
ପ୍ରାୟତଃ 'ମହାକାଶ-ଯୁଗୀୟ ଧାତୁ' ଭାବରେ ପରିଚିତ, ଟାଇଟାନିୟମର ଦୃଢ଼ତା ଏବଂ ଉଚ୍ଚ ତରଳାଇବା ବିନ୍ଦୁ ପାରମ୍ପରିକ ମେସିନିଂରେ ଚ୍ୟାଲେଞ୍ଜ ସୃଷ୍ଟି କରେ। ତଥାପି, ଯେତେବେଳେ ସଠିକ୍ ଉପକରଣ ସହିତ ଖଞ୍ଜାଯାଏ, ଏହା ଏପରି ଡିଜାଇନ୍ ପ୍ରକାଶ କରେ ଯାହା ଜଟିଳ ଏବଂ ସ୍ଥିର, ଯାହା ଏହାକୁ ମହାକାଶ ଏବଂ ଚିକିତ୍ସା ଶିଳ୍ପ ପାଇଁ ଏକ ପ୍ରିୟ କରିଥାଏ।
ଆଲୁମିନିୟମ୍
ହାଲୁକା ଧାତୁର ପ୍ରିୟ ଆଲୁମିନିୟମ, ଏହାର ଚମତ୍କାର ବୈଦ୍ୟୁତିକ ପରିବାହିତା ଏବଂ ନମନୀୟତା ପାଇଁ ପ୍ରସିଦ୍ଧ। ଏହା କେବଳ ମେସିନିଂର ସହଜତା ପ୍ରଦାନ କରେ ନାହିଁ ବରଂ ଓଜନ ବୋଝ ବିନା ଶକ୍ତିର ପ୍ରତିଶ୍ରୁତି ମଧ୍ୟ ଦିଏ, ଯାହା ପରିବହନ ଠାରୁ ପ୍ୟାକେଜିଂ ପର୍ଯ୍ୟନ୍ତ ଶିଳ୍ପରେ ଏହାକୁ ଗୁରୁତ୍ୱପୂର୍ଣ୍ଣ କରିଥାଏ।
ତମ୍ବା
ଏକ ଉତ୍କୃଷ୍ଟ ପରିବାହୀ, ତମ୍ବା ଅନେକ ବୈଦ୍ୟୁତିକ ଏବଂ ଇଲେକ୍ଟ୍ରୋନିକ୍ ଆଶ୍ଚର୍ଯ୍ୟର କେନ୍ଦ୍ରରେ ଅଛି। ଏହାର ପ୍ରାକୃତିକ ଲାଲ-କମଳା ରଙ୍ଗ ସହିତ ଏହାର ବିସ୍ତୃତ ଉପାଦାନରେ ଆକାର ଦେବାର କ୍ଷମତା ଏହାକୁ ଇଲେକ୍ଟ୍ରୋନିକ୍ସ ଠାରୁ ସାଜସଜ୍ଜା କଳା ପର୍ଯ୍ୟନ୍ତ ସବୁକିଛିରେ ଅପରିହାର୍ଯ୍ୟ କରିଥାଏ।
ପିତ୍ତଳ ଏବଂ ପିତ୍ତଳ
ସ୍ୱର୍ଣ୍ଣିମ ସ୍ୱରରେ ଉଜ୍ଜ୍ୱଳ ଏହି ମିଶ୍ରଧାତୁଗୁଡ଼ିକ କେବଳ ସୌନ୍ଦର୍ଯ୍ୟ ବିଷୟରେ ନୁହେଁ। ସେମାନଙ୍କର ପ୍ରଶଂସନୀୟ ବୈଦ୍ୟୁତିକ ଗୁଣ ସେମାନଙ୍କୁ ଏପରି ଉପାଦାନ ପାଇଁ ଉପଯୁକ୍ତ କରିଥାଏ ଯେଉଁଠାରେ ସଠିକତା ସୌନ୍ଦର୍ଯ୍ୟ ସହିତ ମିଶିଥାଏ, ଯେପରିକି ଅଳଙ୍କାର କିମ୍ବା ସୂକ୍ଷ୍ମ ଭାବରେ ତିଆରି ଇଲେକ୍ଟ୍ରୋନିକ୍ ଅଂଶ।
ଆଧୁନିକ ଇଞ୍ଜିନିୟରିଂରେ ତାର EDM ର ପ୍ରମୁଖ ପ୍ରୟୋଗ
ବିଭିନ୍ନ ସାମଗ୍ରୀ ପରିଚାଳନାରେ ଏହାର ବହୁମୁଖୀତା ଏବଂ ସଠିକ୍ ବିବରଣୀ ଏବଂ କଡ଼ା ସହନଶୀଳତା ହାସଲ କରିବାର କ୍ଷମତା ଯୋଗୁଁ ତାର EDM ମେସିନିଂ ଆକର୍ଷଣୀୟ ହେଉଛି, ଯାହା ଏହାକୁ ଆଧୁନିକ ଉତ୍ପାଦନରେ ଗୁରୁତ୍ୱପୂର୍ଣ୍ଣ କରିଥାଏ। ଏଠାରେ ତିନୋଟି ପ୍ରାଥମିକ ପ୍ରୟୋଗ ଅଛି:
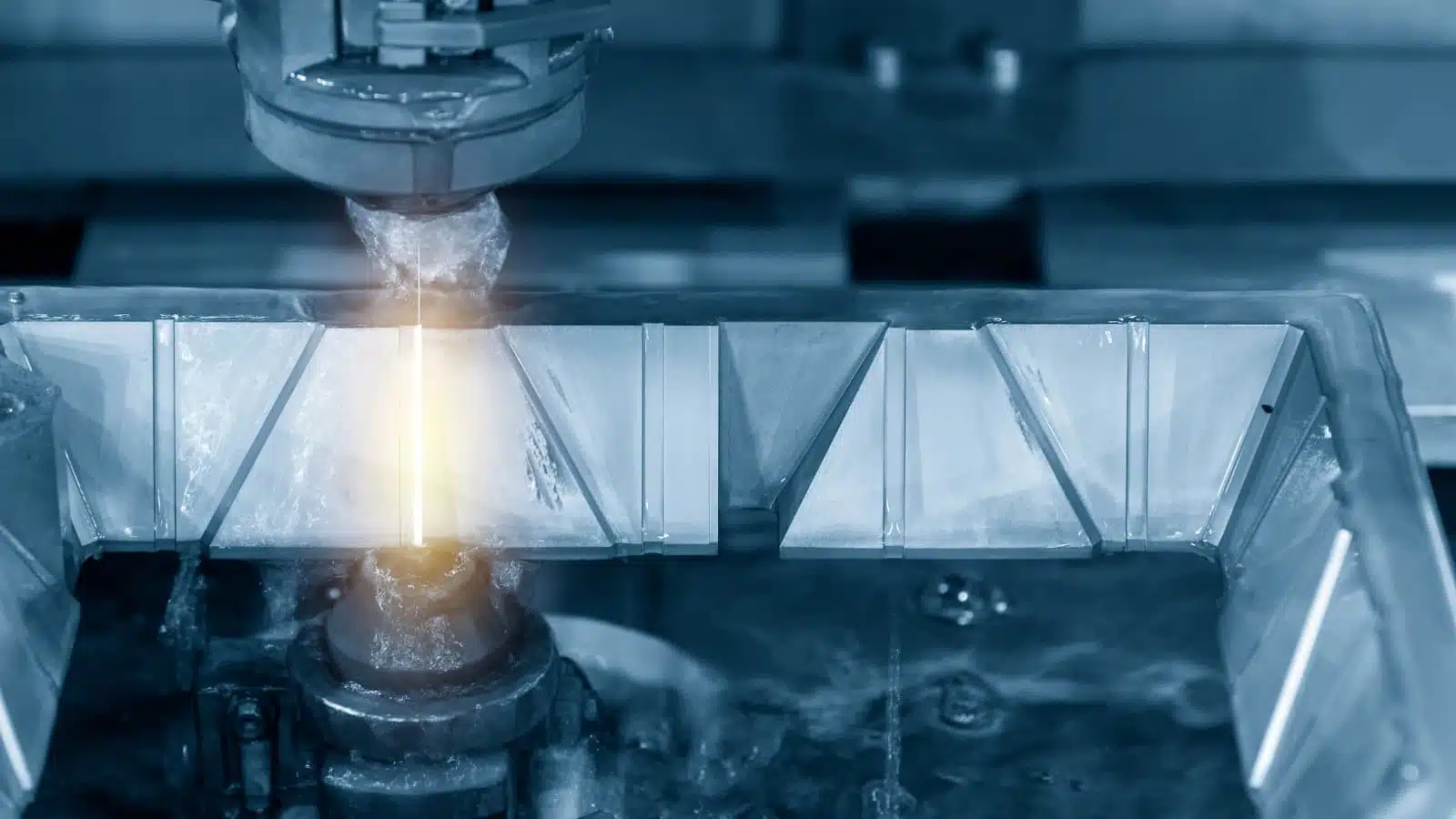
ପ୍ରିସିସନ୍ ପାର୍ଟସ୍ ନିର୍ମାଣ
କଡ଼ା ସହନଶୀଳତା ସହିତ ଉଚ୍ଚ-ସଠିକତା ଅଂଶ ନିର୍ମାଣ ପାଇଁ ସାଧାରଣ ପସନ୍ଦ। ଏହା ବିଭିନ୍ନ ସାମଗ୍ରୀରେ ଜଟିଳ ଆକୃତି, ସୂକ୍ଷ୍ମ ବିବରଣୀ ଏବଂ ଛୋଟ ବୈଶିଷ୍ଟ୍ୟ ଉତ୍ପାଦନ କରିବାରେ ଉତ୍କୃଷ୍ଟ।
ଏରୋସ୍ପେସ୍, ମେଡିକାଲ୍, ଅଟୋମୋଟିଭ୍ ଏବଂ ଇଲେକ୍ଟ୍ରୋନିକ୍ସ ଭଳି ଶିଳ୍ପଗୁଡ଼ିକ ଗିଅର୍ସ, ନୋଜଲ୍ସ, କନେକ୍ଟର୍ ଏବଂ ଜଟିଳ ଛାଞ୍ଚ ଭଳି ଗୁରୁତ୍ୱପୂର୍ଣ୍ଣ ଉପାଦାନ ତିଆରି କରିବା ପାଇଁ ୱାୟାର EDM ଉପରେ ନିର୍ଭର କରନ୍ତି।
ଉପକରଣ ଏବଂ ଡାଏ ଉତ୍ପାଦନ
ଇଞ୍ଜେକ୍ସନ ମୋଲ୍ଡିଂ ଠାରୁ ଷ୍ଟାମ୍ପିଂ ପର୍ଯ୍ୟନ୍ତ ପ୍ରକ୍ରିୟାଗୁଡ଼ିକୁ ପୂରଣ କରିବା ପାଇଁ ୱାୟାର EDM ମୋଲ୍ଡ, ଡାଇ ଏବଂ ସ୍ୱତନ୍ତ୍ର ଟୁଲିଂରେ ଗୁରୁତ୍ୱପୂର୍ଣ୍ଣ ଭୂମିକା ଗ୍ରହଣ କରେ। ସଠିକ୍ ପରିମାଣକୁ ବଜାୟ ରଖିବା ଏବଂ ତୀକ୍ଷ୍ଣ କୋଣ ଖୋଦନ କରିବାରେ ଏହି ପଦ୍ଧତିର ଦକ୍ଷତା ବଡ଼ ପରିମାଣର ଉତ୍ପାଦନରେ ପ୍ରିମିୟମ୍ ଗୁଣବତ୍ତା ଏବଂ ସମାନତା ସୁନିଶ୍ଚିତ କରେ।
ପ୍ରୋଟୋଟାଇପ୍ ବିକାଶ
ଦ୍ରୁତ ଏବଂ ସଠିକ୍ ପ୍ରୋଟୋଟାଇପିଂ ପାଇଁ, ଇଞ୍ଜିନିୟର ଏବଂ ଉଦ୍ଭାବକମାନେ Wire EDM ଆଡକୁ ଆକର୍ଷିତ ହୁଅନ୍ତି। ଏହା ଡିଜାଇନ୍ ବୈଧତା ଏବଂ କଠୋର ପରୀକ୍ଷଣ ପର୍ଯ୍ୟାୟକୁ ତ୍ୱରାନ୍ୱିତ କରେ।
ୱାୟାର EDM ମାଧ୍ୟମରେ ଖଞ୍ଜାଯାଇଥିବା ପ୍ରୋଟୋଟାଇପ୍ଗୁଡ଼ିକ ଶେଷ ଉତ୍ପାଦକୁ ନିକଟରୁ ପ୍ରତିଫଳିତ କରେ, ଉତ୍ପାଦ ବିକାଶ ଚକ୍ରରେ ଏହାର ଗୁରୁତ୍ୱକୁ ଆହୁରି ଦୃଢ଼ କରେ।
ଏହି ମୁଖ୍ୟ କ୍ଷେତ୍ରଗୁଡ଼ିକରେ ଏହାର ଶକ୍ତିକୁ ଦୃଷ୍ଟିରେ ରଖି, Wire EDMର ସଠିକ୍ ଏବଂ ସଠିକ୍ କ୍ଷମତାଗୁଡ଼ିକୁ ଅନେକ ଶିଳ୍ପରେ ବ୍ୟାପକ ଭାବରେ ବ୍ୟବହାର କରାଯାଉଛି।
•ଡାକ୍ତରୀ ଉପକରଣ ନିର୍ମାଣ
•ଇଲେକ୍ଟ୍ରୋନିକ୍ସ ଏବଂ ମାଇକ୍ରୋ-ଉପାଦାନ
•ମହାକାଶ ଏବଂ ବିମାନ ଚଳାଚଳ
•ଅଳଙ୍କାର ଏବଂ ଘଣ୍ଟା ତିଆରି
•ଅଟୋମୋଟିଭ୍ ଶିଳ୍ପ
•ଶକ୍ତି କ୍ଷେତ୍ର
• ଛାଞ୍ଚ ଏବଂ ଡାଏ ମରାମତି
ପୋଷ୍ଟ ସମୟ: ଡିସେମ୍ବର-୧୨-୨୦୨୩